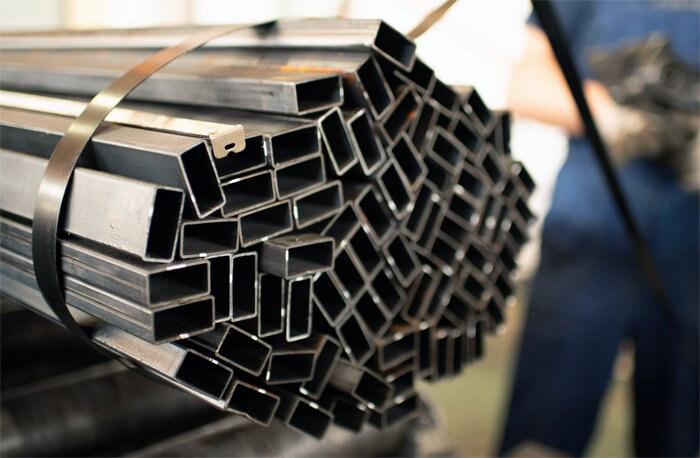
Благодаря развитию современных технологий появился новый способ обработки изделий из металла - плазменная резка металла.
Нагревания металла с помощью электрической дуги недостаточно. В процессе плазменной резки принимает участие ионизирующий газ, который формирует плазменную струю с очень высокой температурой (до +30 000 °C). С помощью такой струи процесс разрезания металла происходит очень точно и быстро.
Для образования плазмы необходимо обеспечить подачу газа в рабочую зону для его контакта с электродугой. Газы используются разные: кислород, водород, аргон и другие. У каждого из них есть свои свойства, которые влияют на конечный результат.
Оборудование для плазменной резки
Для резки металла в данном случае необходим плазмотрон, плазморез и непосредственно плазма.
Плазмотрон
Плазмотрон представляет собой электроприбор, который предназначен для формирования потоков плазмы, контроля и управления ими. Устройство состоит из источника электронов (катода) и электрода, формирующего поле, в котором создается плазма (анода). Они находятся в специальном вакуумном резервуаре.
Катод под воздействием напряжения образует электроны, которые при попадании и взаимодействии с анодом создают электрическое поле в вакууме. Часть электронов в атомах газа под влиянием электрического поля становятся ионами и провоцируют образование плазмы.
Благодаря плазмотрону формируется поток плазмы, раскаляющий металл до запредельных температур, что приводит к плавлению материала. Это дает возможность получить высочайшее качество реза.
Устройство плазмотрона
Разные модели плазмотронов могут иметь некоторые конструктивные отличия, но в целом прибор состоит из следующих составных частей:
-
Электрод. Нужен для проведения высокочастотного тока, создающего плазменную дугу.
-
Насадка для подачи газа, выполняющего аналогичную функцию. Необходима для координации распыления плазмы в месте резки.
-
Кабели, провода. Служат для подачи сигналов и электричества к насадке (соплу) и электроду через блок питания.
-
Расходомер. Координирует подачу и скорость газа с учетом толщины обрабатываемого металлического листа или другого изделия.
-
Держатели. Керамические детали нужны для фиксации сопла и электрода.
-
Охлаждение. Процесс, без которого невозможна работа плазмотрона. Компенсировать большое количество тепла можно с помощью воздуха, жидкости или инертного газа.
Не только конструкция, но и мощность плазмотронов отличается в разных моделях. Прибор может быть дополнительно оснащен электродами и сменными соплами, подходящими для резки разных материалов в зависимости от их толщины.
Плазморез
Плазморез состоит из контроллера, плазмотрона и источника питания. Оборудование предназначено для разрезания металла путем использования потока плазмы высокой температуры.
Под влиянием разогретой плазмы металл в месте реза расплавляется, а удаляет его струя сжатого воздуха.
Плазменная резка может применяться не только для металла, но и для других материалов. Рез выполняется и прямо-, и криволинейно.
Устройство плазмореза
Конструкция плазмореза выглядит следующим образом:
-
Воздушный компрессор. Служит для подачи газа, образующего плазменную дугу.
-
Исполнительный блок. Главная составляющая часть резака, в которой находятся механизм выдвижения и средства управления резаком, а также источник плазменной дуги.
-
Крепление и зажим, благодаря которым резак надежно и устойчиво фиксируется на столе.
-
Система подачи газа. Отвечает за выброс газа в 10-15 см от поверхности. Благодаря такому выбросу стенки не подвергаются воздействию окалин и брызг, а температура не превышает допустимую.
-
Программное обеспечение и компьютер, с помощью которых осуществляется управление резки на всех этапах процесса.
-
Столы для расположения обрабатываемых частей. Бывают стационарными и портативными.
Перечисленные составляющие присутствуют в большинстве плазморезов, но некоторые современные модели дополнительно оснащают системами и функциями, призванными облегчить процесс работы: например, автоматической регулировкой глубинной резки или лазерным указателем.
Виды горелок для плазморезов
В плазморезах применяются разные горелки. Наиболее популярных типов 5:
-
CPG. Электрод и сопло расположены в центре, откуда и подается газ. Этот вид встречается чаще остальных. Центральная подача газа подходит для резки алюминия, металла и нержавеющей стали. Обрабатываемый материал может иметь разную толщину.
-
LPG. Сопло горелки расположено на конце, а электрод – сбоку. Этот тип дает возможность резать только тонкие материалы.
-
Полуавтоматы. Применяются и для ручных работ, и для обработки на станках ЧПУ. Горелки имеют соединение с гибкими трубками, по которым подается газ. Толщина материала может быть любой, что делает этот вид горелок универсальным.
-
Быстродействующие. Отличаются большой мощностью. Их применяют на промышленных предприятиях. Благодаря выделению значительного количества газа горелки наиболее эффективны при разрезании толстых элементов из металла.
-
Ручные. Повсеместно используются в столярных мастерских. Их сфера применения – тонкие детали.
Предпочтительный вид горелки выбирается с учетом габаритов обрабатываемого изделия, типа резака и требований, которые предъявляются к резке.
Плазма
Плазма – это особенное состояние веществ, которое можно считать пограничным между твердыми телами или жидкостью и газом. Процесс ее образования выглядит следующим образом:
-
Через электрическое поле, находящееся между плазмотроном и электродами, проходит газ, в который подается электрический разряд.
-
Газ ионизируется.
-
Формируется плотный поток плазмы высокой температуры.
В результате взаимодействия плазмы с металлом производится гладкий рез, с которого испаряются капли расплавленного металла.
Газы, применяемые для плазменной резки
Для плазменной резки применяется целый ряд газов, поэтому перед выбором одного из них необходимо учесть свойства и особенности применения каждого вида.
Водород
Подходит для разрезания толстых металлов, поэтому часто применяется на предприятиях тяжелых отраслей промышленности. Водород обеспечивает высокую температуру образующегося пламени.
Этот газ легче многих других, что ускоряет его движение в потоке плазмы. Это свойство дает возможность резать металл быстрее. Благодаря теплопроводности водорода резак охлаждается, предотвращая перегрев инструмента.
Из минусов газа выделяется его взрывоопасность, что может спровоцировать трудности в работе с ним. При использовании водорода необходимо применять повышенные меры безопасности, чтобы предотвратить взрыв.
Аргон
Относится к категории инертных газов. Аргон не вступает в реакцию с металлом и в достаточной степени охлаждает его, поэтому часто применяется для разрезания тонких листов. Газ влияет на улучшение качества реза и сводит к минимуму вероятность окисления металла.
Аргон отличается низкой стоимостью и является наиболее доступным по сравнению с аналогами, но имеет один неоспоримый недостаток – его можно применять только для тонкой резки. Для взаимодействия с толстыми изделиями придется выбрать другой газ.
Азот
Эффективный, доступный и качественно режущий газ. При работе в условиях высоких температур и давления отличается стабильностью. Азот обеспечивает низкую вероятность окисления металла. С его помощью можно разрезать металл любой толщины.
Есть у этого газа и несколько недостатков, главный из которых – вероятность образования в процессе работы оксида азота, который отрицательно влияет на здоровье. Кроме того, азот стоит дороже воздуха и аргона.
При соблюдении требований безопасности применение азота не несет никакой угрозы человеку.
Кислород
Важное свойство кислорода – высокая температура его горения. Эта характеристика делает его максимально подходящим для плазменной резки. Жидкий кислород подается в струю плазмы через специальный канал. Его газообразная форма достигается при прогоне через оборудование.
Высокие температуры кислорода позволяют прожечь металл насквозь на большую толщину. При этом кислород по сравнению с другими газами (водородом, аргоном и другими) более доступен.
Недостаток кислорода в том, что он характеризуется высокой взрывоопасностью, поэтому использовать его нужно только при постоянном контроле. Оператор плазменной резки должен быть профессионалом своего дела, который применяет специализированное оборудование.
Сжатый воздух
Наиболее часто используется при плазменной резке как дополнительный газ. Благодаря многим свойствам является подходящим для применения в плазменном резаке. Основные плюсы сжатого воздуха – это доступная цена и легкость получения из любого компрессора. Сжатый воздух дешевле азота и аргона, поэтому его применение является экономически более выгодным.
Высокое содержание азота в воздухе (около 78%) под воздействием высокой температуры может спровоцировать образование оксида азота, который относится к токсичным газам, отрицательно влияющим на здоровье человека.
Относительно небольшое содержание кислорода (около 21%) может привести к потере качества реза, поэтому сжатый воздух проигрывает по этому показателю другим газам.
Особенности процесса плазменной резки
Плазменная резка требует напряжения в 220 В, если речь идет о небольших резаках, и 330 В – в случае работы промышленного оборудования, позволяющего делать рез на материалах большой толщины.
Весь процесс резки можно разделить на несколько этапов:
-
Подготовка. До начала работ необходимо позаботиться о месте, где они будут проводиться. Рабочая зона и резка должны быть выбраны с учетом масштаба предстоящего процесса и характеристик металла (его типа и толщины).
-
Образование плазмы. Для формирования плазмы необходима газовая горелка, благодаря которой между анодом и катодом появляется электрическая дуга. В рабочую область попадает газ, превращающийся под действием ионизирующей дуги в плазму.
-
Контроль горелки. Оператор, работающий с плазменной горелкой, постоянно следит за ней, меняя скорость и движение резки. Сама горелка должна находиться на расстоянии нескольких мм от поверхности металлического изделия. Это обеспечивает контакт плазмы с поверхностью, приводящий к ее разрезанию.
-
Нагревание. В момент максимального приближения горелки к металлу происходит сильное нагревание поверхности изделия, которое приводит к разложению металла на свободные электроны и ионы.
-
Резка. При движении горелки вдоль изделия нужно поддерживать скорость, температуру и глубину реза. В таком случае происходит расплавление и разрезание металла.
-
Окончание резки. Когда процесс реза заканчивается, горелку убирают от поверхности изделия. Дуга гасится.
Использование метода плазменной резки позволяет выполнять резку точно и эффективно, оставляя чистый рез без зазубрин.
Разновидности плазменной резки
Процесс плазменной резки выполняется одним из трех способов:
-
Механизированная. Резаки монтируются на механизированные станки с ЧПУ. Плазморезы управляются через специальное программное обеспечение, с помощью которого они перемещаются и осуществляют резку по точно заданным параметрам. Такой метод выбирают на крупных производствах и больших заводах, где необходима не только высокая точность, но и скорость реза.
-
Ручная. Резак выполнен в виде пистолета, которым вручную управляет оператор. Этот способ наиболее применим на маленьких предприятиях и в мастерских, где на первом месте – удобство, компактность и мобильность.
-
Мультитул. Представляет собой целый комплекс инструментов в одном агрегате. Может выполнять также сварку и другие виды обработки поверхности. Современные мультитулы являются роботизированными и используются на масштабных предприятиях и крупнейших заводах.
Плюсы и минусы плазменной резки
К преимуществам метода можно отнести следующие:
-
Скорость. Благодаря высокой скорости работы улучшается эффективность и уменьшаются производственные затраты. Время обработки деталей ощутимо сокращается.
-
Универсальность. Плазменную резку можно использовать для разных типов материалов и большого количества металлов: меди, алюминия, стали, титана и других.
-
Стойкость к деформации. Резка не оказывает давления на материал, поэтому ее использование не приводит к механической деформации металла.
-
Качество. Рез, который получается под воздействием плазменного потока, выходит аккуратным и не требует дополнительной обработки.
-
Возможность обработки толстых деталей. С помощью плазменной резки можно разделять даже металлические листы толщиной 20 см.
-
Минимальные затраты на обслуживание. Оборудование требует периодической чистки и практически не нуждается в замене расходных деталей и материалов.
Есть у метода плазменной резки и ряд недостатков:
-
Риск искрения. Во время работы оборудования возможно образование искр, что опасно при наличии рядом легковоспламеняющихся предметов.
-
Громкость. Процесс работы довольно шумный, что может мешать.
-
Дороговизна расходных материалов. Для обеспечения резки оборудование нуждается в периодической смене электродов и сопла.
-
Затраты на покупку. На приобретение плазмореза придется потратиться. Чем выше оснащенность установки, тем больше она будет стоить.
-
Выбросы в атмосферу. В результате плазменной обработки могут образовываться токсичные газы и пыль. Чтобы нейтрализовать их воздействие, необходимо четко соблюдать все меры безопасности.
Рез прямого действия
Рез может быть прямым или косвенным. Прямой рез встречается чаще. После обработки остается одна линия разреза, поскольку плазма двигается в заданном направлении и не меняет его. Резак, который используется в данном случае, выглядит как горелка с соплом и электродом.
Плюсы реза прямого действия:
-
Качественный рез. Отличается гладкостью, поэтому применим для большинства типов производства.
-
Использование новейших технологий. Управление процессом осуществляется с помощью современного программного обеспечения, что обеспечивает высокое качество реза.
-
Скорость не в ущерб качеству. Наряду с возможностью быстро производить обработку одновременно достигается высокая точность реза с соблюдением заданных параметров и способностью воздействовать на материалы большой толщины.
Рез косвенного действия
Такой рез формируется путем скашивания на обрабатываемом изделии. Для получения скоса нужно дополнительно использовать насадку, которая двигается по вертикали. В момент обработки материала плазменный поток попадает на материал не прямо, а под углом. С учетом насадки угол наклона может отличаться.
Плюсы реза косвенного действия:
-
Увеличенная площадь контакта плазменного потока с поверхностью материала. Достигается за счет скоса реза и позволяет минимизировать деформацию и сделать обработку более точной.
-
Улучшенная прочность. Скошенный рез положительно влияет на материал, укрепляя его и делая более прочным.
Метод косвенного реза применяется во многих тяжелых отраслях промышленности, в том числе в судостроении, строительстве мостов и других крупных объектов, а также при производстве радиаторов.
Плазменная резка дает возможность обрабатывать металлические изделия разной толщины, включая профили и трубы, изделия из титана, алюминия, меди, стали, алюминия и других металлов.